我们知道无论是单螺杆挤出机,或是双螺杆挤出机,其螺杆均悬臂安装于挤出机的机筒中,螺杆在旋转状态下将物料推向出料口。料流在整个输送的过程中,不断地接受由机筒孔壁传递的热能,同时也不断地获得因受螺棱剪切作用而得到的剪切热。在这二个热能的作用下,高分子材料迅速地或被塑化,或被反应。所有针对挤出机机筒螺杆工况条件的分析,我们均离不开对这个高分子材料在挤出机内被塑化,被反应的基本状况的分析。
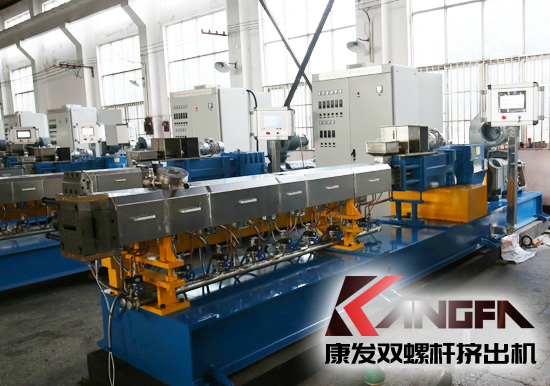
既然螺杆悬臂安装于挤出机的机筒中,那么螺杆的挤出段螺棱表面金属材料与机筒内壁金属材料之间就一定存在二者之间的“接触磨损”,或可称之为“匹配磨损”。众所周知的是,同种金属材料之间的“接触磨损”,或可称之谓双向匹配“摩擦副”是*糟糕的。例如机筒和螺杆均采用渗氮钢的材料制造,而且经过相同的氮化处理工艺手段,其量化的“匹配磨损速率”显然*糟糕。
这个“匹配磨损”情况的严重性在大型挤出机中表现得之所以更为突出,是因为螺杆自身较大的重量,例如外径为217毫米,长径比达33的螺杆,其重量约1.4吨。这个大型的重达1.4吨的螺杆之相当的质量,随着螺杆的旋转而不断地以螺棱表面金属材料摩擦机筒内孔表面金属的形式,不断地威胁着挤出机的使用寿命。
讨论
双螺杆挤出机的机筒螺杆工况,我们还不能或视的另外一个重要因素是,与普通单螺杆挤出机的螺杆相比较,双螺杆挤出机的螺杆为组合形式,物料的输送,即这个扭矩的传递是依靠直径相对较小的芯轴。由于芯轴的直径有限,因此其强度有限,螺杆工作状态的非直线性显得更为严重。这个非直线工作的螺杆在聚甲醛反应挤出机的液相反应区间几乎在“扫膛”机筒内孔壁,金属材料之间的“匹配”摩擦剧烈程度是相当异乎寻常的。而比较一般的配混改性挤出,由于有粘性较大的高聚合物料包裹于螺杆外围,使得螺杆在正常工作中往往能够“自悬于中”,这样还能够适当减轻这个“匹配”摩擦的矛盾。然而在共聚反应挤出中,往往缺少这个“自悬于中”的物料的保护,聚合机内部的这个“匹配磨损”现象比普通配混挤出就显得更为严峻。
相对于机筒内壁,因为螺杆的螺棱表面积要小得多,剧烈的“匹配磨损”所造成的“磨损减量”,在反应挤出段的螺棱顶部表现得更为突出,螺杆的螺棱外径受磨损而迅速明显变小。当挤出机的核心部件之机筒螺杆均采取同种渗氮钢材料制造,并且表面都是经过同种的渗氮硬化处理,由于渗氮后的硬化层厚度仅仅为0.40~0.70毫米,一旦这个有限的硬化层被突破,机筒内孔表面及螺杆的螺棱表面的“磨损减量”将明显加快,挤出机在一个相当短的时间内即产量迅速下降,反应挤出过程的温度在短期内即变得难以控制。
我们讨论共聚反应挤出与配混改性挤出的工况条件之不同点,还必须侧重提到温度控制在不同挤出机上的重要性。由于共聚单体在反应挤出中的放热,在经过混合,熔融,脱气,再混合等反应过程中时,整个连续共聚合反应链对温度相当敏感,达到33长径比的挤出机各工作区段对温度要求非常严格,处于相变的二个相邻区段的工作温差甚至可以达到70℃以上。如果机筒螺杆磨损严重,机筒和螺杆的螺棱之间的间隙增大到一定程度,在双螺杆螺棱啮合程度降低和挤出背压作用下,料流在挤出机内部将表现得相当无序,混乱而不稳定,所有上述提到的聚合过程严格的温控要求将无法实现。当温度越来越难以控制,作为反应挤出机的*终产物之聚合物的达标质量就将完全失控。
由于螺杆的螺棱向前推送物料,则表现为其不断地剪切料流,那么挤出机在正常运行状态下就存在着第二类磨损,即螺杆对料流的“剪切磨损”。这个“剪切磨损”的程度除了与料流中的增强剂和填充剂等添加成份的比例成正比外,还与料流的粘度成正比。由于共聚反应挤出中,料流中一般没有或很少有额外的增强剂和填充剂的加入,但是物料的粘度却比较高,二者叠加的剪切磨损矛盾与配混改性挤出相比较表现较弱,因此与上述*类的“匹配磨损”情况相反的是,反应挤出机中的螺杆“剪切磨损”与一般配混改性挤出相比较就显得不那么突出。
某些高分子材料在受热塑化,或反应放热的过程中会释放出一定的腐蚀气体,该腐蚀气氛会腐蚀挤出机的机筒和螺杆,这是我们分析机筒螺杆工况条件的一个不可忽缺的重要因素。值得庆幸的是,例如在聚甲醛的“本体共聚合”连续反应挤出中,基本不存在挥发性腐蚀气体的逸出,因此机筒螺杆工作表面的被腐蚀可以不作工况条件的深入讨论。