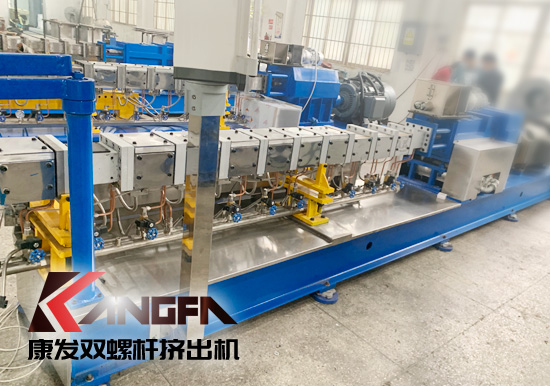
汽车制造行业所需塑料品种繁多,聚丙烯(PP)复合材料是主要品种之一,其用量占汽车塑料使用量的1/3以上。但因降解、氧化等原因产生大量挥发性有机物(VOCs),造成车内环境质量下降,限制了PP材料在高档汽车中的应用。
车用PP复合材料气味来源分析
车用PP复合材料气味的来源复杂,从基材的聚合到复合材料的改性加工再到运输、储存、使用等过程都会有散发性气体产生。
首先PP原料在聚合时,存在己烷、乙醇、庚烷等溶剂和部分小分子聚合物的残留。
其次,加工过程中需要添加催化剂、助剂。如能增加两相相容性的增容剂;提高耐刮擦性能的耐刮擦剂;增强光热稳定性的抗氧剂和光稳定剂等。添加的催化剂和助剂基本都属于小分子化合物,这些小分子化合物赋予了PP复合材料更加优异的加工性能和应用性能的同时也对PP复合材料的异味有一定的贡献。
最后,在加工过程,如注塑、挤压加工改性时,PP在高温高剪切加工下由于自由基的断裂以及分子歧化反应产生醛、酮等散发性气味。PP分子链上含有极不稳定的叔碳原子,在光、热、机械等外界作用下发生降解释放一些散发性物质。
车用PP复合材料气味控制技术
01 PP粒料的选择
为了满足轻量化、薄壁化的零件设计要求,PP改性材料要求较高的流动性,即较高的熔体流动速率。当前生产高流动PP粒料方法有氧化降解法和氢调法。
氧化降解法工艺简单,可操作性强,但在气味方面存在缺陷。
而氢调法通过氢气浓度对PP粒料的流动性进行调节,不会产生强烈的异味物质,在车用PP粒料的生产中逐渐受到青睐。由于分子量调节剂氢气反应活性低,对催化剂的要求较高,工艺尚不十分成熟,但也有不少企业取得了一定的进展。
将加氢法和氧化降解法生产的树脂制备的复合材料进行VOCs含量的对比测试,
02 助剂的选择
PP材料在汽车上的应用有主副仪表板、门板、立柱等零件。为满足不同零部件对材料特性的要求,通常会加入各种助剂。助剂的加入改善了PP复合材料的性能,但同时也给PP材料带来了气味问题。究其原因,或是因为有些助剂自身的气味,又或是因为加工过程中的高温降解,生成一些气味物质。
汽车主副仪表板、门板、立柱等具有外露面的零件,对材料的耐刮擦性要求较高,因此在生产这些零件时需加入耐刮擦剂进行性能优化,常见耐刮擦剂主要有聚硅氧烷类和酰胺类。
部分PP材料中采用过氧化物作为分子量调节剂,产生新的气味问题。传统的过氧化物如氧化二异丙苯、二叔丁基过氧化物等在高温下易分解成醛、酮等异味分子。而采用二叔戊基过氧化物与PP树脂混合制成母粒,可有效降低过氧化物降解带来的气味问题。
PP若发生氧化反应,会导致材料变黄、硬化等不良现象。而通过加入抗氧剂,可以捕捉自由基形成稳定产物,延长PP材料使用寿命。有研究表明,不同类型的抗氧剂挥发性不同,挥发性随相对分子质量升高而降低,可以选择高相对分子质量的抗氧剂作为降低气味的手段之一。
PP复合材料用助剂种类复杂,选择合适的助剂对材料的气味改进效果是明显的。助剂的优化可从以下三个角度出发:一是助剂在低浓度下的高效性;二是助剂与基材良好的相容性且不与复合材料其它组分反应、不影响复合材料的其它性能;三是高热稳定性、低挥发性、无异味。
03 吸附剂除味
添加吸附剂是提升PP改性材料气味的有效手段之一。吸附剂除味主要分为化学反应和物理吸附。
化学反应是指在PP材料中加入特殊的螯合剂,使其与易挥发物质发生螯合反应。由于反应产物的分子量较大,不易挥发出来,从而锁定了异味成分。化学吸附主要依靠物质间的化学键,即需要吸附剂和气味物质产生一定的化学反应,因此化学吸附的针对性特别强,适用于挥发性物质种类少且明确的情况下。
物理吸附主要是采用多孔结构物质,利用其大量的结晶空洞对气味分子或挥发性的小分子进行吸附,常用的物理吸附剂有氧化铝、活性炭、硅藻土、凹凸棒硅胶、分子筛等。
物理吸附和化学吸附从其吸附除味原理来看,应用中各有限制,为增加吸附效果目前产业中将多种除味剂进行复配使用的较多。由于吸附剂的种类多样,吸附原理和作用不同,对PP材料本身的物性影响也有不同,因此,在实际生产加工中,需要进行多轮的试验、小批量验证,最终优选最佳的吸附剂选用方案。
04 萃取–脱挥技术
吸附型除味技术是将气味分子以化学或物理形式吸附,从而减少气味分子的挥发。而萃取型除味则是通过加入挥发性强的萃取剂,萃取剂通常为低沸点化合物,利用萃取剂与气味小分子共沸原理,将气味分子脱离PP材料。
当前常用的萃取剂有水、低分子醇醚、含水的聚合物母粒以及表面活性剂等。从萃取型除味原理来看,萃取除味技术通常需结合PP材料造粒过程中的抽真空,即脱挥技术来提高除味效果。一般在PP材料改性造粒生产过程中,采用的是双螺杆挤出机。双螺杆挤出机的剪切较强,且可以分段执行不同功能,有剪切区和推进区之分。在推进区可以将部分螺杆区域开孔、开槽,和抽真空设备一起形成脱挥区。多阶脱挥装置在合成、混炼、造粒的过程中脱除小分子物质,从而减少加工过程中的副反应。而萃取剂在熔体中快速挥发运动,进一步加快了小分子的脱离。
脱挥效率在一定范围内随着真空度的增加而提高,同时增加萃取剂的用量,也能促进PP改性材料中挥发物的散发速度。但过大的真空度会导致生产成本的增加且当真空度达到一定值后,也即当吸附–解吸附达到平衡后继续增加真空度,对脱挥效率基本无明显提高,真空度的选择需跟进生产情况综合考虑。
05 后处理条件的选择
在PP改性造粒过程中,温度一般在230℃以上。在这个温度区间,PP材料本身已开始分解。同时,在高温条件下,PP和助剂会产生复杂的聚合和分解反应。PP的分解产物和助剂参与反应的副产物,是PP材料加工过程中新产生的小分子物质,会明显影响材料的气味状态。因此,需要针对这些小分子材料,通过增加烘烤后处理的方式,有效地使其挥发,减少其对材料的气味影响。
目前,主流的改性厂家,均采用烘料罐的形式,对粒子进行烘烤后处理。部分生产厂家,甚至会采用多轮烘料罐的形式,增加烘料的时间和烘料的均匀度,进一步增强小分子异味的散发。
文章来源:工程塑料应用
免责声明:任何个人或组织若对文章版权或其内容的真实性、准确性存有疑义,请第一时间联系我们。我们将及时进行处理及删除!康发双螺杆挤出机感谢您的关注!