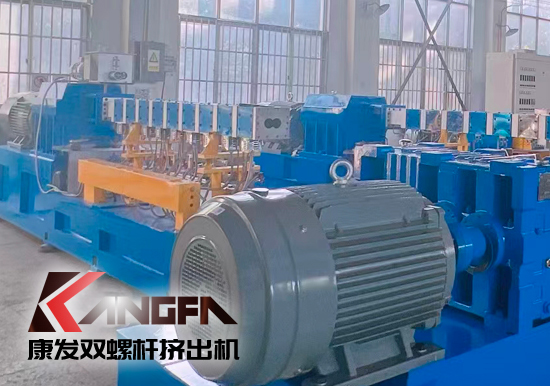
为了达到所要求的物理性能,排气是配混聚合物与添加剂和填料所需要的几种操作之一。最终产生的粒料混合料,必须是没有空隙和残留的挥发物,否则就会导致挤出或注射成型部件中产生缺陷。
大多数的
双螺杆造粒机配混除了一个真空排气口用于挥发物排出外,还利用一个或多个常压排气口(例如,在侧喂料机处用于去除夹带的空气)
配混商必须认识到客户的一台单螺杆造粒机,通常没有任何排气能力,粒料内的任何挥发物质只能在成品部件中释放出来,导致表面缺陷、孔等。对于易水解或由于吸湿导致分子量降低而发生降解的聚合物,在配混过程中进行高效率的排气是获得合格物理性能的关键。
根据工艺要求,造粒机机筒内的排气口可在常压或真空下操作。最典型的配混过程包含两种排气。挤出机可以配备多个真空排气口,用于去除大量的溶剂或单体,使成品中的残留挥发物保持在低水平。
针对同向旋转双螺杆造粒机,多种排气口设计得到了开发,以适应各种应用和材料。这些设计包括排气口加料器、延伸的排气机筒和侧排气口等,且得到发展,克服了标准排气口(位于挤出机机筒的顶部)设计的一些问题。
有可供选择的排气口设计,以适应脱气的具体要求。由于聚合物在排气口积累和降解时会产生污染,因此加热的侧排气口具有防污染的设计
无论是在常压下还是在真空下,排气稳定运行的要求是螺杆在排气区域保持低填充水平,在上游区域是高填充水平起到“熔体密封”的作用。
排气问题可分为两类:
1. 操作上的问题,即聚合物(和/或其他原料)流出挤出机排气口。这个工艺问题通常需要操作人员介入来清理排气口或者关闭生产线。
2. 由于挤出机机筒内的排气不足,造成残留的挥发物/气体仍留在配混的粒料内。在这种情况下,需要提高排气效率,以生产出合格质量的产品。
出现这两个问题的原因,以及它们相应的解决方案是什么呢?
为什么料从挤出机排气口中流出来?
这类问题对于所有的双螺杆配混挤出机都是很常见的。常压排气口被设计成在聚合物初始熔融后排放空气、水分和其他挥发性气体。气体和/或蒸汽从排气孔中流出的速度是一个体积流量和排气口面积的函数。
当蒸汽流速太高(由于体积太大或开口面积太小的缘故)时,排出的气体会夹带固体,导致熔体流出排气口。这可以通过增加排气口面积,并可能需要增加排气口来解决。
对于粒子填料(滑石粉、矿物填料、碳酸钙等)侧向进料到熔融聚合物中,需要常压排气口排放通过侧喂料机与粉末一起进入机器中的空气。填料的体积密度越低,则进入挤出机机筒必须排放的空气就越多。如果排气口面积过小(相对于必须被清除的空气体积),则产生的高出口速度往往会把微粒和粉末带出排气口。解决这一问题需要扩大排气口面积,如前面所提到的,可能还需要增加排气口。
以高含量(高达80%)和高生产率侧向喂入低体积密度填料需要多个常压排气口,以方便从挤出机机筒中排出大量的空气
在第一个侧喂料机处存在未熔化聚合物也会导致填料流出与侧喂料机相关的排气口。要诊断这是否是该问题的根源,就必须在侧喂料机相关排气口处进行熔体质量的物理检测,以验证是否存在未熔化的树脂。如果有未熔化的树脂,则需要修改螺杆上游部分(用于聚合物熔融)的设计。
真空排气口的位置通常是在造粒模头的附近,被用来在真空条件下排放任何残留的蒸汽。熔体从真空排气口流出并阻碍排气口,这似乎是一个非常普遍的问题。当这种情况发生时,气体不会从熔体中除去,导致挤出的粒料带有孔隙呈现多孔状。排气口堵塞需要操作人员手动清除,在某些情况下可能还需要关闭生产线。
对于这一问题,几个可能的原因和解决方案如下:
当滤料网或模头压力增加时(例如滤料网被污染物堵塞时),阻塞长度相应增加,直到到达挤出机机筒的排气口。此时即使没有真空,熔体也会从排气口连续流出。解决这一问题的办法是减少压力(如增加滤料网的面积或模头孔的数量/大小),并通过把真空排气口移动到机筒上游(或在真空排气口后增加一段机筒)或者安装一台熔体泵加压下游设备,来提高挤出机的输送长度。请注意,这些解决方案往往需要花费大量金钱。
当机器末端处的挤出螺杆元件磨损时,将会发生同样的情况(阻塞长度到达真空排气口)。因此,在螺杆磨损的情况下,熔体常常会随着时间推移越来越频繁地流出排气口,并最终成为常态。此种情况下应该直接更换磨损的元件。
当阻塞长度(填充螺杆的长度以形成压力)到达真空排气口时,熔体就会从真空排气口中流出。阻塞长度增加是滤料网结垢或模孔冻结造成的结果。螺杆和机筒筒体在这个区域内的磨损随着时间推移也会造成并加重熔体流出,最终导致排气口溢流成为常态
如果熔体密封元件的支撑压力小于真空压力,则熔体也会流出真空排气口。这是因为真空泵是在挤出机机筒内抽吸空气,导致熔体被“抽”出机器。因为没有在挤出机机筒上安装压力传感器,所以找到问题原因的唯一线索是观察真空表。如果真空表随时间推移是稳定的,那意味着真空系统是“密封的”;如果仪表数值降低,则说明空气被抽出系统(排气口将充满熔融塑料)。如果熔体仅在真空时流出真空排气口,说明真空密封元件没有产生足够的压力。针对真空密封,改变螺杆的设计,使用更多的限制元件是唯一的解决办法。
熔体在填充段之间暴露于真空;最大可支持的真空水平取决于上游熔体密封的压力(如果熔体压力小于1atm)
在高温下暴露于真空时,有一些特殊的材料会表现出独特的性质。这些材料在到达机筒口时往往膨胀和发泡,不会轻易流回到螺杆中。当使用常规的排气口时,这些材料总是会流出机器。因此它们只能在真空下使用安装在排气口的排气加料器来加工:加料器的机械双螺杆系统防止熔体在挤出机螺杆槽外面膨胀,并允许气体轴向移动通过排气加料器的螺杆。
机械
双螺杆造粒机排气口加料器被用来防止熔体在真空下运行时被抽出挤出机螺杆槽。排气口加料器可以安装在侧面(如图所示)或者挤出机机筒的顶部
为什么没有更多的东西排出排气口?
如果当前的机器配置、排气口设计和操作条件不能够除去足够数量的挥发物,那么这些解决方案通常是修改螺杆的设计和/或机筒的配置。
利用真空从熔体中除去挥发性气体,并为物料传输提供附加的推动力。大多数的配混生产线在100~300mbar(1mbar=0.1kPa)的真空压力范围内操作。通过采用以下解决方案,可进一步提高脱出挥发物的能力:
1.如果真空条件下的熔体滞留时间是限制因素(扩散限制),那么一个选项将是减少出料量,以增加平均滞留时间。这不是一个常用的选项,但却是最容易实现的。
2.另一个增加滞留时间的解决方案是把熔融密封元件重新定位在挤出机机筒内更远的上游。真空部分也因此可延伸到更远的上游。
3.增加真空度至最大的限度,这通常需要更换现有的真空泵系统。
4.通过增加输送元件的间距来减小真空部分的填充程度。螺杆槽中较低的填充会产生较薄的熔融层,气体得以通过该层扩散。
5.用附加的真空排气口重新配置机器。如果现有的机筒中没有足够的L/D来包含一个二次真空排气口,则需要增加当前机筒的长度。
6.将冷却水注入真空排气口机筒上游,以减少挥发性物质的分压。